706 Madison Avenue
706 Madison Avenue, New York, NY 10065
Yong Yue
Structural Option
BUILDING STATISTICS

General Building Data
Building Name
Location
Occupancy
Size
Number of Stories
Construction Dates
Cost
Project Delivery Meothod
706 Madison Avenue
706 Madison Avenue, Manhattan, New York
High-end Retails
48491 SF
5 floors above grade | 7 total levels
Mar. 2015 - Jan. 2017 (Under Construction)
$1000/SF (Estimate)
Design-Bid-Build
Owner
Architect
Construction Manager
Structural Engineer
MEP Engineer
Primary Project Team
Architecture
Figure 1 - Elevation Northeast
(Courtesy of Friedland Properties)
The 3-story existing building (landmark) is converted from a bank to high-end retail, with a five-story horizontal extensions on two sides. (See Figure 1 & 2) There are two design goals that the architects are trying to fulfill: to meet the historical requirements for the landmark, and to maximize the interior space for retail. In order to meet the historical requirements, the facade of the existing building (exterior) could not be altered and the new enlargement’s exterior had to be designed to match existing. Additionally, architects redesigned the interior space with emphasis on improving the functions for retail stores. Main columns are removed (3B,3B,4B) from the ground floor of the existing building. Elevators, stairs, corridors and MEP rooms are placed as close together as possible (shown at left and bottom of the Figure 2) to provide more space for retails use. Other functional components and design include two additional entries for access to both E 63 Street and Madison Ave and a roof top garden (Discussed in sustainability section below)
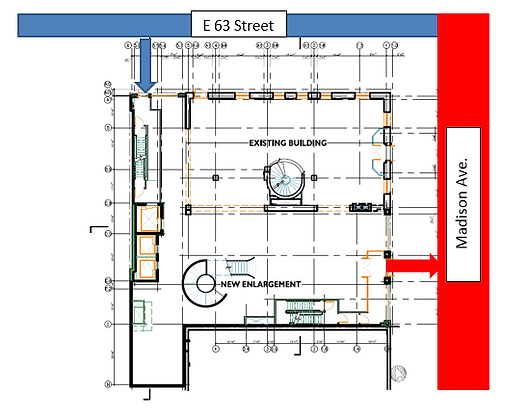
Figure 2 - Ground Floor Plan View (courtesy of SGH)
Codes, Zoning & Historical Requirements
-
Code:
New York City Building Code (NYCBC), 2008 with Current Revisions ASCE 7 - 02 Minimum Design Loads for Buildings and Other Structures
-
Zoning:
C5-1: Special Madison Avenue Preservation District (MP) preserves and reinforces the unique retail and residential character of Madison Avenue and the surrounding area from East 61st to East 96th Streets. Retail continuity is ensured for the famed specialty shops by mandating that the ground floor of buildings on Madison Avenue must be occupied by selected uses. Bulk and street wall provisions limit the height of new development to the scale of existing buildings but allow for greater lot coverage. The maximum floor area ratio is 10.0. The location and setback requirements for street walls of buildings fronting on side streets provide a smooth transition to the lower buildings typically found on the midblocks.
-
Historical Requirements:
The existing building was constructed in 1920’s and has been a landmark building in New York City. It is protected under the Landmark Law and a very important part of the City’s heritage and that LPC(Landmark Preservation Commission) must approve in advance any alteration, reconstructions, demolition, or new construction. Especially for the exterior of building, like facades, exterior walls and other enclosure systems, if you want to perform minor work or make alternations to the exterior of building, you must obtain the Commission’s approval before you begin the work. However, it comes up with some exceptions. For example, the ordinary exterior repairs and maintenance, like replacing broken window glasses or removing small amounts of painted graffiti don’t require a permit, and also the interior work generally does not require LPC review. The Commission has approved such proposals when the design of the new building was found to be appropriate to the character of the historic district.
Building Enclosure
Based on the historical requirements, if a designer wishes to work on or change the design of the addition the Commission would require that the work make the addition less intrusive and more appropriate. Therefore, the exterior enclosure of the addition has been designed in a way to match the existing building’s enclosure, which consists of a typical brick facade, double-hung aluminum-clad wood windows, flat brick arched lintels, marble string course, marble cornice, slate mansard roof, etc. The addition building uses a limestone belt and string courses to align with the existing marble cornice and marble string course. It also uses a limestone cornice and metal spandrel panels to align with the cornice and spandrel at the adjacent building. At the ground floor, the addition’s main entrance has been profiled with thermally broken bronze storefront framing assembly with ½” fully tempered glazing. (Figure 3)
Roofing has been designed with insulated double lock standing seam zinc, ice & water shield membrane, 2” POLYISO rigid insulation board. The terrace roof consists of lightweight porcelain paves, tapered POLYISO rigid insulation board sloped to drain, ‘UNI-JUST & STAK-CAP’ pedestal system on buffer pad and double layer TPO membrane at all roof drains.
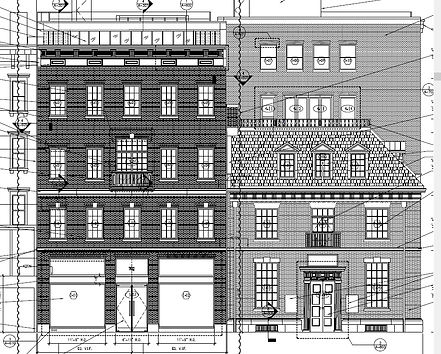
Figure 3 - Elevation East (courtesy of SGH)
Sustainability Features
As shown in Figure 4, a roof garden was created at the top of the existing building not only to interact with the addition but also to provide a space for eating, drinking, relaxing and entertainment. Since the building is at the corner of Madison Ave and E 63 Street, which has the historical neighborhood and popular shopping stores, it will be a perfect sport to see daily life in the upper east Manhattan area. In addition, Lighting design also takes place on the roof garden. LED recessed in-ground lighting is used along the stainless steel handrail assembly, and a 42” glass railing is located behind the balusters.Mechanically, the walkouts and windows between the addition and the garden roof also provide natural ventilation where air can flow from E 63 street side to the Madison Avenue side.
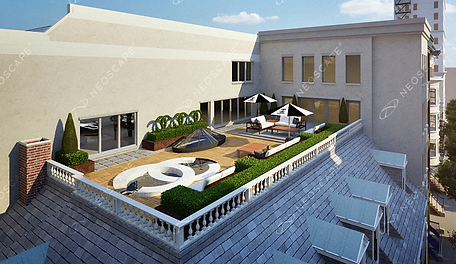
Figure 4 - Roof Garden (courtesy of SGH)

Figure 5 - Roof Plan
(courtesy of SGH)
Figure 5 shows that a skylight system (yellow) will be added on the new enlargement’s roof. Five double sloped glazing systems with raised concrete or CMU curb will be located in the middle of the roof, and single sloped glazing system will be added between the sloped standing seam metal roofing in front of the roof.
Structural Systems
-
Existing:
The superstructure above grade consists of structural steel beams, girders and columns. Floors are comprised of 1 ½” 18 GA. composite metal deck with 3 ¼” lightweight concrete topping supported by wide flange beams. Typical bays are 28’x30’ wide with W14x22 beams and W16x31 girders. The foundation of the existing building is a mat foundation. The lateral resisting system of the existing building is contributed by the exterior masonry walls and an interior masonry stair.
The superstructure of the addition consists of structural steel beams, girders and columns. The addition adopts similar slab/deck for floor system; however, it uses 3” 16 GA. metal deck to accommodate longer slab span. The critical bay is 16”x29” with W18x35 beams and W16x31 girders. Columns sizes range from W10x33s to W14x605s. The foundation system of 706 Madison Avenue addition is comprised of a 2’-6” thick mat slab reinforced at the top and bottom. The lateral resisting system of the addition is steel moment frames.
-
Addition:
Mechanical Systems
The building has very minimal mechanical systems in order to condition the required spaces, such as mechanical and electrical rooms, until the building is fit-out in the future. A heat pump on the sub-cellar level with cooling capacity of 30 MBH and a heating capacity of 32 MBH, coupled with an air cooled condensing unit on the roof, serves elevator machine room on the sub-cellar level. There is a general supply fan, with a 15 KW duct heating coil, and general return fan located on the sub-cellar level that provide heating and 600 CFM of ventilation for the mechanical and electrical rooms on that level. There is also an exhaust fan on the roof to exhaust 600 CFM of air from the restrooms on the cellar level. Multiple unit heaters of three different sizes, 5 KW, 7.5KW and 10KW, are provided on every level in order to keep the interior of the building at 65 degrees. There are duct risers and roof-top areas reserved for the mechanical systems of future fit-outs.
Lighting/Electrical
Fluorescent and LEDs are majority used in the most space of the building. Lighting design in this building is focused on meeting the basic functionality and efficiency, instead of pursuing an aesthetically appealing design. There are only six fixtures for the whole building. And the most common fixture is a 1’x4’ fluorescent fixture that is surface mounted. The emergency lighting doesn’t look to be compliant of the 1:40 uniformity ratio.
Since it’s a retail outfit. The lighting design would be cheap and simplistic. Once the tenants move in they will do their own lighting design and when they move out, they have to put back in what were there. The cheapest and so few fixtures have been used in this building, because they are just to be used between tenant fit-outs and to meet the minimum requirements for lighting design. In addition, this building has some nice skylights for good daylighting, which tends to improve the scales rate of the store that have access to that daylight.
This building has secondary service (electricity is supplied to the building at the building utility 1208/120V). It has a 3 phase 1200kVA transformer to bump up the voltage to 480/277V for the mechanical equipment. Each tenant space is switched separately so they can charge each tenant for the electricity they use.
Construction
Construction on 706 Madison Avenue began in March 2015. The building (addition) is still under construction and will be finished in January 2017. The construction of new addition was challenging due to constrained site conditions. The building has two below grade stories, with new excavation adjacent to historical townhouse. Because of multiple unforeseen conditions including tangent-pile wall misalignment, below-grade protrusions at the adjacent buildings, and high ground water, the construction team has to work inside of the site and the foundation and the lateral resisting system of the addition need to be re-designed several times as the construction proceeded. The project delivery method is Design-Bid-Build. The project has a construction management team with individual contractors.
Engineering Support Systems
-
Fire Protection:
Basic floor systems in the building requires a 2 hour fire rating, while bearing walls and similar assemblies require a three hour fire rating. Passive fire protection material insulate steel structures form the effects of the high temperatures that may be generated in fire. They can divided into two types, non-reactive, of which the most common types are boards and sprays, and reactive, of which thin film intumescent coatings are the most common example. This building is made of steel, so it has include one to the passive fire protection type mentioned above. In addition, an active fire protection system, which includes automatic fire detection and fire suppression are installed throughout the building.
-
Transportation
One service elevator and two passenger elevators are located in the west end of the building and extend from the basement to the fifth story. Two main stairs are located in the west end and south end of the building. A circular stair is located at center of both the addition and existing building to support a heavy transportation during the shopping time. Walkouts between the addition and existing to support building circulation between two buildings.